MNRSIM: A Research and Training Model of the McMaster Nuclear Reactor
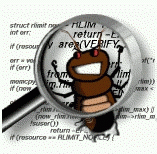
BUGS!
MNRSIM is a ongoing project and is currently filled with bugs. You can
help by documenting problems and e-mailing the authors.
Known Problems with MNRSIM
General Issues
- MNRSIM is built using very basic physical models, and
many of these models have not yet been verified. Anyone who can supply
concrete data which describes the actual behavior of light water type
reactors is encouraged to submit testing scenarios.
- Water neither freezes nor boils in the model.
- Although water flow can be reversed in the core, heat transport is
coded for one direction only.
- Many controls are present but inactive on each of the control panels,
inactive controls are planned features which are currently either not
working correctly, or not implemented at all.
Control Panel
- The power control is over simplified and not realistic.
- The calibration lock state sometimes does not save correctly.
- Calibration is confusing, and too complicated.
- The control rod positions should lock when the simulation is
running.
Core Panel
- Energy Group settings for the core display and plot sometimes do not
indicate the group being displayed.
- Table view also has same indication problem.
- Defined cells MUST have 4 character names. This limitation should be
fixed.
- Cannot destroy the plot or core display window with standard windows
close button.
- Core orientation is not indicated in any way.
- Core is not labeled in the same way as the MNR core. For example, MNR
core uses Letters for one axis, numbers for the other.
Thermal Hydraulics Loop 1
- Red blinking light indicates the detection (and partial correction) of
numerical errors in the heat transport method. The correction is a fudge,
and a better numerical integration method should be installed.
- The HC Iter window shows which module is currently active. Normally
this label should flicker quickly between each module, HC= Hardy Cross,
HTP=Heat Transport, HTF=Core Heat Transfer. If it gets stuck on a single
setting, the simulation is probably spending too much time in that
module.
- The core heat transfer module sometimes exhibits odd behaviour, for
example the initialization flag is often locked, but not always, core
elements can be selected when time=0, but not at other times. The fuel
plate selector doesn't always seem to be doing anything (although it is).
The Z axis selector is sometimes left at 1, which produces a flat
temperature distribution in the plate since this is the first plate.
The module does work, although it isn't 100% intuitive how it works.
Thermal Hydraulics Loop 2
- The air temperature is currently used as the lowest temperature in
the simulation for error detection. If the air temperature is set higher
than the default temperature (20 deg C.) bad things will happen. If
the air temperature is set lower than 0, pipes may spontaneously freeze.
Fixing the heat transport model will remove this limiation.